Custom Hardwood Floors
Custom hardwood floors, what is custom about hardwood floors? What is considered
custom?
Is it a border? No, anyone can purchase borders, premade designs and just install
them - easy.
Is it a medallion? No, these are made on a cnc machine, again, anyone can purchase
these same designs and install them - easy.
Mix materials? ehhh, still can be duplicated by anyone - still easy.
Although, many will consider these above designs custom. They can be easily duplicated,
therefore it wouldn't be custom. Simply, because it wouldn't be unique or one of a
kind.
The point of having a custom made hardwood floors, is so no else, will have the same wood
flooring as you. Because they're unique and one of a kind, that's bragging rights for
anyone who owns a custom hardwood floor.
So, what is custom hardwood floors?
Well, if you can find a rare wood specie that no one can get their hands on, and have
wood flooring made, that's a custom hardwood floor.
If, you can have some insane border design custom made, like your name in five different
wood specie with diamond inserts. Yeah, that's custom hardwood floors.
And how about a medallion, that has your own image in five different wood species, with
some bling. You would probably like that.
I think your starting to get the picture of what custom made hardwood floors are. It's
something no else will have, not because they can't afford it. But rather they won't
think of it.
In this article, I will explain how to design, layout and construct a custom curved
hardwood border, Along with pictures of custom hardwood floors from our project. If, you
want any of the above ideas, you'll have to send it out to a CnC shop, so they can put it
on a Cad/Cam system. Too much for me to cover here, how to use Cad/Cam, setting up and
operating Cnc's, so back to the article.
So, Let's begin...
Flooring Tool List
- Miter Saw
- Table Saw
- Jig Saw
- Belt Sander with 80 grit belt
- Finish nailer and compressor
- Orange Builders string or anything to layout shape of curve
- Material to make jig for arc, this can cardboard cut to 3"x40" strips, 3"x40"luan
strips, or plywood.
- Pencil
- Chalkline
- Quick clamps
- Framing Square
- Tape Measure
- Finish nails
- 6 foot level or straight edge
- Flooring material
- 3/4"x8" sq. stock (be sure that this material matches your flooring material)
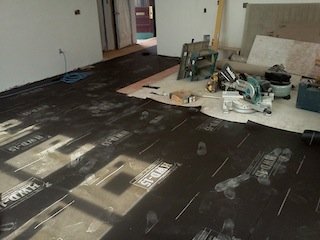
Start by laying out your
underlayment or vapor barrier. Staple the ends down, so they don't get in the way or
shift on you, while you're trying to lay out your design.
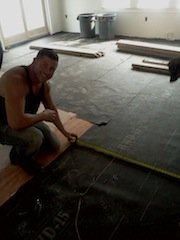
Once the underlayment is in place,
begin to layout your curve. Don't worry it doesn't have to be perfect. You just need to
position and see how big of a curved border you would like.
In this photo, Mark from BB Unique Remodeling is here to finalize size and location of
the custom hardwood floor curved border. We had to put in consideration of cabinets and
furniture locations, so do the same when your laying out your custom made hardwood floors
design.
Once you have your locations figured out, use the builders string to layout your curves.
Move and adjust the strings as needed, until you get a layout that is visually
comfortable to you.
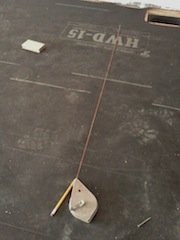
Now, that you have your rough
custom hardwood floors curved layout. It's time to draw in a hard layout. Start with
simple lines, lines should be parallel and straight. Use your tape measure and straight
edge to do this.
Once, you have your lines in place, it's time to find the center points for your arcs.
Using a tape measure, measure from the end point of the arc to the center, to get your
radius value, be sure to measure from both end points.
Round off your measurement to the nearest inch or feet. Keep your numbers simple, use
measurements at 1, 1 1/2, 2, 2 1/2, 3, 3 1/2 ft. etc.
This will help you with your addition and subtraction, keeping them simpler to figure
out. Once you have a radius value, using the framing sq. measure from the end point to
the center, measure from both endpoints. The intersecting point is your center point for
your radius, place a nail here. Draw and arc using your chalkline anchored to the nail,
make a rough drawing of the arc.
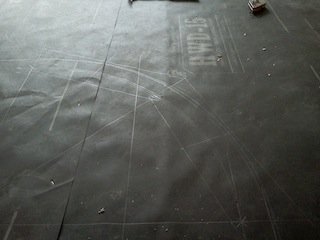
After, you have drawn in your arc
for your custom hardwood floor border design. Decide how many segments, you will need to
create the arc. For example on a full corner radius, with arc swinging from a horizontal
line to a vertical line.
If, you want this to be 2 segment or 2 piece, then divide 90/2 = 45 degree, you'll need
cut 2 pieces, with side angles at 22 1/2 degrees. For a 3 segmented arc or 3 pieces, it
would be 90/3 = 30 degrees, you'll need to cut 3 pieces with side angles at 15 degrees.
The number of segment or pieces needed will be determined by the width of your border,
stock size, and size of arc.
On our project we decided on a 2 piece arc, so our angle was 45 degrees with 22 1/2
degree per side.
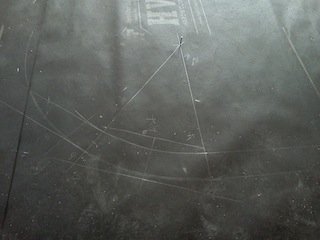
Next, we need to figure out, our
stock width, for our custom hardwood floors curved piece. Fortunately, we only have to
figure out dimensions for only, one segmented piece, the second piece will be the same, a
mirror.
Start by drawing a line from midpoint(Id -inside diameter) to midpoint(Od - outside
diameter) on your arc. Extend the line pass the Od by 1/2", using a framing sq., draw a
perpendicular line, the width of the arc. Offset the line, to the endpoint of the Id of
the arc, add and additional 1/2". You now, have a Length and Width dimension, for your
segment of your arc.
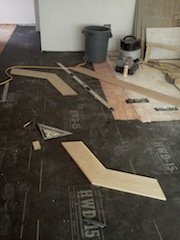
Cut your pieces out and do a dry
layout. As long as all your figures are correct, you'll end up with an pieces, with the
length to size and the width will be oversized.
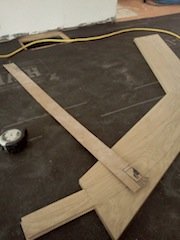
Using a strip of 3"x 40" material,
in this photo, I used a piece of cardboard, that was waste. You can use any type of
material, improvise, if possible. Create a story stick, template to draw your arc. You
should have a hole for the center point and holes for your Id and Od.
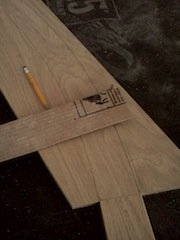
With the hardwood stock in place,
draw your arcs, onto the material. Be sure that your lines are visible.
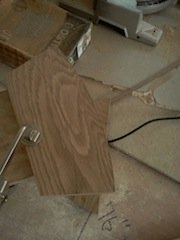
Using your jig-saw, cut out your
arc, leaving it 1/16" or more, oversized.
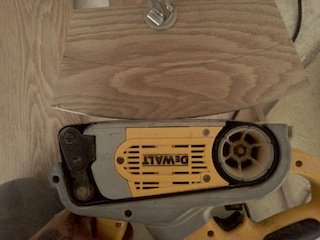
Using your belt sander, sand your
arc into dimension, check the cut side for squareness to the top surface. Check the
width, to make sure there within tolerance and at the width you want. Our arc was cut to
2 1/4", the same width as our flooring. By doing this, we saved ourselves work from
having to create the straight boards.
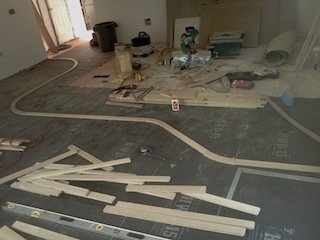
Once all your pieces are
fabricated, dry fit the pieces, make sure they fit properly and the width is continuous
from start to finish. Once satisfied, nail in your arcs first, then your straight boards.
Use a finish nailer, to face nail them in place.
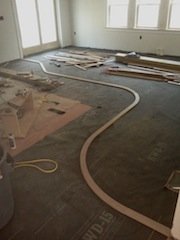
You've now created a one of a kind
hardwood floor design, a custom hardwood floors border. You can say you have custom
hardwood floors made.
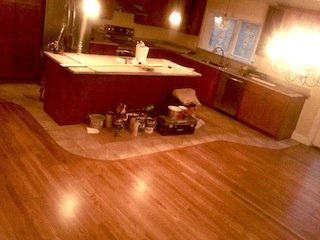
If, you can build one of these, you'll be able to build anything. You can add custom
inlays to bring the design to another level. Unlock your abilities, you have more
capabilities, then you know.
G and S wood floors
Lynn,Ma.
Google+